Manufacturing ERP Software: Why it is Important to Have One?
Operational efficiency is constantly sought after in a dynamic industry such as manufacturing. Here manufacturing ERP becomes the game-changer. The system offers a centralized platform where one source of accurate, real-time information is used for managing every aspect of facility operations and processes. It provides unprecedented visibility and improved coordination across disparate business processes, allowing manufacturers to proactively manage manufacturing operations, speed up decision-making, and prevent disruptions or delays.
With the inclusion of advanced tools and technologies, manufacturing ERP systems now has become smarter, faster, and leaner, and they are better equipped to keep pace with the rapid business changes. Thus, ERP in the manufacturing industry promotes efficiency and increases productivity while reducing administrative and operational costs.
What are Must-have Features in Modern Manufacturing ERP?
ERP plays a pivotal role in stimulating manufacturing business profits, however, it is worth considering that not every software has the same calibre. Understanding and adapting features that could drive the transformation makes a remarkable difference in the software performance and the productivity of your business you are looking for. Here are the six capabilities that need attention while evaluating your modern manufacturing ERP software.
Track and trace lot batches
Storing multiple types of raw materials and processed goods in the warehouse could create confusion among employees leading to misuse of stock or leftovers. Therefore, the primary and indeed one of the most significant features to look for in a manufacturing ERPis to have 360-degree visibility of inventory.
This means your ERP needs to include inventory management tools capable of providing end-to-end traceability, from purchasing raw materials and half-processed products to the finished goods available in each lot. Real-time information also helps shop floor supervisors see the quantity of raw materials and finished goods and know where they are stored. This enables you to maintain proper inventory levels and address probable issues in advance, saving potentially severe repercussions.
Inventory cost tracking
There is no denying that material cost takes up a large share of manufacturing expenses. Purchasing raw materials beyond manufacturers' current needs could take a toll on their financial health. Adopting a leaner inventory management approach could save businesses from investing in unnecessary materials.
For this, your ERP has to include an apt cost-tracking feature. It has to be capable of tracking the expenses of manufacturing a particular product by calculating the cost of the ingredients required depending on the quantity of raw materials used and other charges associated with the special storage conditions needed for sensitive material, and so on.
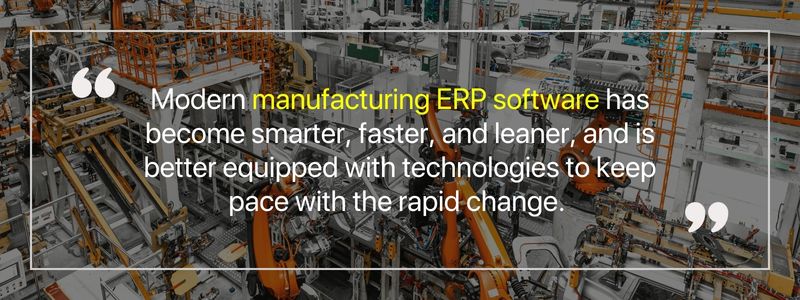
Supply chain optimization
Supply chain optimization is a critical task, and its primary advantage is establishing good relationships with vendors to ensure that quality raw materials reach your warehouse to produce superior products at reasonable prices.
Your ERP software needs to include the intelligent supply chain management feature that aids in monitoring and controlling the supply of raw materials to meet the demand for finished goods. An optimized supply chain also guarantees that the production and distribution of your products are performed efficiently and cost-effectively.
Swift production schedule adjustment
What would you do if your customer demanded a particular product that is not in your production line? Would you be able to quickly deliver their request or reject it as re-working your current setup would take a lot of time?
A robust manufacturing resource planning software with agile production scheduling capabilities would support this. It would assist you in planning production ahead of time and rescheduling plans as needed to increase business efficiency and make the most of your resources. The system would also allow you to run an inquiry and check your inventory status. If you have sufficient stock on hand, you could immediately reschedule production plans and put the requested product on the line, or else raise purchase orders and start production immediately after raw material reaches your warehouse.
Complete quality management
Maintaining product quality in all lot batches improves customer satisfaction by constantly delivering quality goods, which in turn provides long-term success to manufacturing businesses.
Your manufacturing ERP needs to include quality management capabilities to ensure that goods are produced while maintaining excellence. The system could be used to define the quality check parameters and continuously monitor and measure the product quality at every stage of the production process. The objective here is to eliminate flaws and increase efficiencies so that the production goes right the first time.
Compliance with government regulations
Every industry requires following the government-defined set of rules and regulations, which businesses must remain in the foreground to avoid the likelihood of compliance issues. However, constant updates in these regulations make keeping a tab on them challenging.
An Advanced ERP system would facilitate tracking these new and changing rules that might be difficult to maintain manually. Deploying an ERP application with such a feature would support you in remaining compliant with laws and industry standards as they change over time.
Business Success with Manufacturing ERP Software
When finding the right ERP for manufacturing business, consider getting a system with the above features.
As one of the leading industry-ready ERP solution providers, we are well-versed in the different business challenges and could help guide you toward choosing the right system to solve them. Connect with our software experts to learn more about the services we provide. Fill in the form and get started!